|
Henkel presents high performance lightweighting solutions at Composites Europe
9/18/2015 |
|
|
Latest developments in high performance composite matrix resins, binders and release agents, composite adhesives, process know-how and engineering, will be presented by Henkel in the Composites Forum at the Composites Europe exhibition at the Messe Stuttgart on September 23. Henkel will place a strong emphasis on its expertise in developing cost-effective solutions for automotive structural components, such as lightweight leaf springs produced using high-pressure resin transfer molding, HP-RTM.
Fig. The rear axle of the new Volvo XC90 features a new transverse leaf spring, made of lightweight composite material.
Henkel is a full composites solutions provider for the automotive industry, offering not only matrix resins and tailor-made adhesives for production and assemblies of composites parts, including hybrid concepts incorporating metal components, but also in-depth process and engineering know-how in RTM from its own technical centers around the world.
Loctite MAX 2 polyurethane matrix resin
The Loctite brand is probably most commonly associated with market-leading consumer and industrial adhesives, but the range also includes ground-breaking products for use as matrix resins in high performance composites, increasingly used in structural automotive components. Henkel's flagship product, Loctite MAX 2 two-component polyurethane composite matrix resin system, enabled automotive composites specialist Benteler-SGL to develop the highly innovative RTM glass fiber reinforced leaf springs now used on Volvo's premier crossover SUV, the XC90.
"Loctite MAX 2 stands out in particular for its extremely fast cure and its high flexibility and toughness," says Frank Kerstan, Global Program Manager, Automotive Composites, at Henkel. "This enables the high-speed production of composites with excellent durability, exactly the sorts of features required in parts such as the Volvo leaf spring."
Breakthrough application in lightweight leaf springs
Used in place of traditional steel coil springs for the rear suspension, the RTM composite leaf spring enables a massive weight saving of 4.5 kg compared to the traditional concept. Composite leaf springs, have many advantages: the elimination of the coil springs and suspension struts for example means that the axle protrudes less into the trunk area, leaving more loading space. Volvo is expected to use the technology in more of its cars in the future, and other manufacturers are also developing similar axle concepts.
The RTM process for the Volvo leaf springs was developed jointly with Henkel's process know-how, which is key for large scale manufacturing. The production system installed at Benteler-SGL, which uses a multi-cavity tool, is designed for a production output of over 100,000 pieces per year.
BENTELER-SGL mass-produces the composite leaf springs for the rear suspension using Loctite MAX resin from Henkel. (Photos: Henkel, PR004) Excellent processability for short cycles
The Loctite MAX 2 polyurethane system has very low initial viscosity, which enables fast injection of the resin into the mold and excellent penetration between the tightly-packed reinforcing glass fibres. Once injected into the mold, Loctite MAX 2 cures very quickly, much quicker than standard epoxy resins, for demold times as low as one minute per part.
In use, the flexibility and excellent toughness of Loctite MAX 2 has a positive effect on the fatigue behavior of composites under load, even under exposure to widely varying temperatures and significant exposure to moisture, oil or other media. A leaf spring, for example, is exposed to constant dynamic stresses when the car is in motion. Loctite MAX 2 ensures a very long service life of the component, even under very adverse conditions.
"For the automotive industry particularly, process know-how, integration and matching products within an overall package is essential for this lightweight technology," Kerstan says. "Henkel is therefore working hard on further developing resins, binders and multi-substrate adhesives, that can be incorporated within new composite concepts and contribute to optimizing the production process."
Industrial adhesives for bonding multi-material assemblies
Apart from its Loctite MAX matrix resin systems, Henkel industrial adhesives are increasingly used in the automotive industry, for bonding lightweight materials. Especially in the area of modern lightweight body designs, adhesive bonds can replace traditional welded and riveted joints for dissimilar substrates. They also help to reduce noise, seal gaps, and smooth out production fluctuations.
Henkel is targeting numerous other applications in automotive and other industrial sectors with its high performance composites matrix resins and adhesives. These include structural parts such as body components, exterior paintable parts such as a roof, and chassis and powertrain components, including wheels and drive shafts. Frank Kerstan will discuss progress with polyurethane matrix resins in enabling large-scale production of automotive composites, in the Composites Forum taking place during Composites Europe. The presentation, which will use the Volvo leaf spring as a case study, is scheduled for 10 a.m. on Wednesday, September 23 in Hall 5 Booth B42.
More information about Henkel Composites is available at www.composite-lab.com. |
|
Related Exhibition:
|
|
|
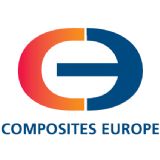 |
|
Composites Europe 2015
|
10th European Trade Fair & Forum for Composites, Technology and Applications
9/22/2015 - 9/24/2015
Venue: Stuttgart Trade Fair Centre, Stuttgart, Germany
|
|
|
|
|
|
|