|
|
FLASH Cartesian Robots
|
|
Smooth integration
This handling device is an accessory that must ONLY be installed and integrated on NEGRI BOSSI plastic material injection presses (prior to checks aimed at ensuring the press software has been updated), since the control system requires CAN Bus network connection with the network units of the press itself without the classic EUROMAP 12 cabled connection..
This level of integration, in addtion to allowing the user to maintain an unaltered level of extraction device (handler) safety, provides considerable ADVANTAGES with regard to the information that the press and the handling device are able to exchange.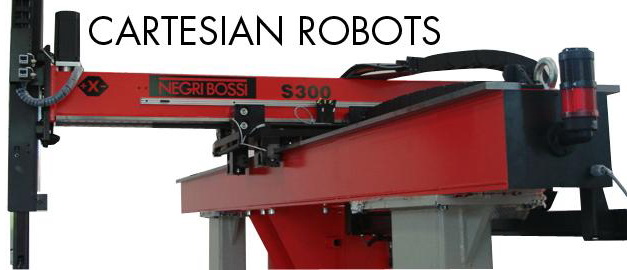 The robot control system is integrated with the machine control system; this ensures greater operating simplicity:
cycle settings.
storing programmes on the machine.
supervision of robot operation.
online maintenance (AMICO).
process data acquisition.
The standard programming interface features a user-friendly self-learn function that allows for easy, simple robot set-up, even where the operator has no specific programming knowledge.
Press-robot ontegration simplifies and improves coordinated control of the whole, ensuring greater working safety and shorter cycle times. The robot features a portable control unit for manual commands and programming of the work cycle in self-learn mode. In addition to setting and checking the cycle, it is also possible to consult all the robot data (diagnostics, times, press-robot consensus etc.) and save or load the robot file with the machine moulding file.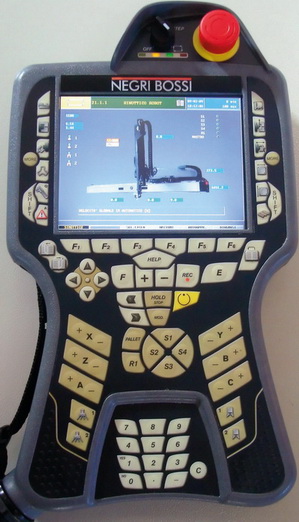 Main characteristics
NEGRI BOSSI robots are available in 7 different versions: S50 - S100 - S200 - S300 -S400 - S500 -S600, one suitable for presses up to 320 tons with single-section vertical arm, and others up to a 2500 tons, equipped as standard with vertical telescopic arm. Like the other axes, the vertical arm is motor-driven by a rack and pinion; a belt drives the frontal arm at double speed. Robots are supplied with a portable control unit for manual commands and self-learn programming tasks. All versions feature the same press software package, including the pre-set work cycles for both Simplified mode (with standard piece pick and place cycles) and Libera programming mode (for more complex work cycles and management of peripheral automation units).
Mechanical elements have been designed to eliminate vibration on the pick-up head, provide high torsion rigidity and a long working life. The mechanical structure is based on a main steel beam, an extruded aluminium extraction axis beam of large cross-section, a simple vertical (S50-S100) or telescopic (S 200-300-400-500-600) structure and a cast aluminium plate that houses all three robot axis gearmotors. All movements are obtained by way of a rack and pinion system and each axis features two recirculating ball bearing guides with four slides. On the standard version the power panel is mounted directly on the robot to minimise the necessary floor space. Optimised weight distribution, together with accurate acceleration control - achieved via digital drivers and brushless servo-motors - allows very high shift speeds and extremely accurate positioning, efficiently resolving any in-mould insert placement problems.
Thanks to an air manifold and an electrical connector on the vertical axis tube near the pick-up head, the latter can now be replaced more quickly.
The air circuit connectors are of the fast type and any pick-up head electrical connections are made using a quick-release socket/plug coupling.
Thanks to the 90? tilt that can be obtained with the pneumatic axis ????and 180? ??/B??rotation of the pick-up head, it is possible to establish, using a ''wrist effect'' movement:
the orientation with which the approach to the object to be manoeuvred in the mould is made;
pick-up from fixed and/or mobile surface;
any required rotation in the mould area for shifting of of intermediate figures with double and/or triple injections;
rotation, where necessary, after pick-up in the mould area, to prevent any collisions (mould cooling pipes, piston parts on mould, gate covers etc);
adjustment of extracted pieces at external stations where pieces need to presented in a certain way;
deposit of pieces in the required position;
pre-assembly of extracted pieces on the deposit platform;
presentation of the extracted piece in specific positions for shearing of the sprue, cutting of the piece and/or a part of it;
Consequently, this wrist-like movement effectively provides a wide range of pick-up/extraction/deposit movements.
Movement of the wrist(s) is provided by pneumatic drivers (which run on compressed air) or, on request, controlled-rotation electrical drive.
In conclusion, then, the FLASH handling unit provides:
Outstanding rigidity thanks to the V-guides with coupling, at several carriage points, with recirculating ball bearing runners;
High speed and acceleration thanks to rack and pinion devices;
Fast replacement of the pick-up head thanks to the air manifold and electrical connector near the head itself on the vertical axis;
Extreme FLEXIBILITY: thanks to integration of numerical axis control, PLC and control panel it is possible to programme, in complete freedom, the work sequence most suitable for the specific application;
PRECISION positioning thanks to numerical control of the axes by networked digital drive;
Outstanding REPEATABILITY of axis positioning on account of very high rigidity and numerical control;
POWER, thanks to top-of-the-range brushless motors;
Simultaneous movement of 3 axes;
Simple SELF-LEARNING of required pathways by carrying out manual movement of the axes and saving the effected sequence/cycle;
PALLETIZATION for programmable pallet loading;
NUMEROUS programme-controllable accessories and devices;
DIAGNOSTICS of Robot alarms on press; |
|
Related Products |
| BI-POWER TWO-PLATEN CLAMPING PRESSES SACMI IMOLA S.C. Small, compact injection moulding machine: thanks to its 2-platen closing system and 2-cylinder injection assembly the design is smaller than on an in-line ... | | Bi-Power Two Platen Machine Negri Bossi SpA A range of two-platen machines from 1,200 to 6,000 tonnes.
Small, compact injection moulding machine: thanks to its 2-platen closing system and 2-cylinder ... | | Systec - powerful and energy-efficient. Sumitomo (SHI) Demag Plastics Machinery GmbH The Systec is a hydraulic injection moulding machine from the European product range of Sumitomo (SHI) Demag. It is characterized by sturdy and compact ... | | El-Exis - Benchmark in High-Performance Fast-Cycling Sumitomo (SHI) Demag Plastics Machinery GmbH The El-Exis sets tomorrow?? standards of precision and speed. Extremely fast travel and injection cycles are easily achieved without sacrificing in precision ... | | Zero-moulding with SE-DUZ, SE-HSZ and SE-HDZ Sumitomo (SHI) Demag Plastics Machinery GmbH High precision and high process stability are becoming more and more important. Thanks to direct servo-motor drive and intelligent servo-motor control, ... |
|
|
|
|