|
|
Jomar Injection Blow Moulding Machine (IBM)
|
|
Injection blow moulding is designed to create plastic bottles and containers that meet exacting standards with consistent weight, volume tolerance and quality.
It produces more finished bottles per cycle per hour without deflashing and trimming.
Our injection blow moulding machines are used globally in many applications; from personal care, medical, cosmetic, automotive, food and household uses etc.
We provide single source injection blow moulding systems, from mould design to complete machines, 15 to 175 tons, with a level of productivity to suit your production needs.
Our injection blow moulding machines are capable of processing a variety of materials including HDPE, LDPE, PP, PS, PVC, K Resin, PET, PETG, SAN and Barex in some cases without even changing the screw. However, some materials require additional machine features: Fan cooled barrels, Heated core rods, material drying etc.
Our advanced features include:
Total machine control system with color terminal bottles and containers from 2 ml to 2 litres
All-new proportional hydraulic system on larger machines
Totally enclosed moulding areas
On-screen troubleshooting and diagnostics
Training tailored to meet your requirements
What it does
The injection Blow moulding (IBM) process produces billions of plastic containers each year. Ranging in size from 1 ml to 2 liters, these containers meet exacting standards of consistent weight, volume and tolerance, and are popular around the world for a myriad of applications from pharmaceuticals to toiletries to automotive to household use.
What it costs
Compare an injection Blow moulding machine to a similarly priced extrusion Blow moulding machine: With IBM it is possible to produce more bottles per cycle and more bottles per hour without deflashing, trimming, re-granulation and re-mixing of scrap, at a constant weight and with injection moulding tolerances. In fact injection Blow moulding does not produce a significant amount of scrap polymer, many companies are using virgin materials continuously.
How it works
The heart of the injection Blow moulding process is a triangular rotary table, which indexes in 120? steps. Core rods mounted on the face of the table form the inside of the hot parison (or preform) that is later blown into the finished container.
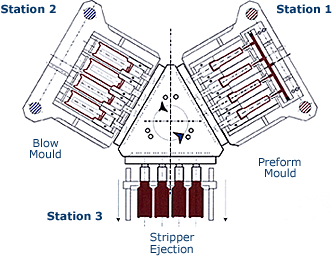 Station 1: This is the preform mould. Here, molten material is injected under low pressure into the mould cavity, where it forms a parison around the core rod. At this stage, the neck section is injection moulded to close tolerances. After suitable conditioning, the moulds open and the parison is transferred on the core rod to...
Station 2: This is where the blow takes place. The cavity of the mould defines the shape and finish of the container. The parison is blown with air fed internally through the core rod. As the blown plastic contacts the cold blow mould, the final moulding is produced. The mould opens and the finished bottle is transferred on the core rod to...
Station 3: Here, the bottle is stripped from the core rod for packing or filling.
Why Jomar & IBM
The Jomar Vertical Plastifier uses typically 1/3rd less energy than a horizontal reciprocation screw.
It is possible to make from 1 - 32 bottles per cycle. Cycles start at about 9 seconds for 10ml bottles, up to 20 seconds for technical parts and the larger containers.
Many standard materials can be moulded: HDPE, LDPE, PP, PS, MIPS, PVC, PET, PC, Barex, K Resin, Santoprene, PU etc. Some materials require drying, fan cooled barrels, screw changes, heated core rods etc. Ask Jomar for this information and on processing engineering resins
Machines range from Model 15 - 175 with a vertical plastifier. The M65 - M175 can be equipped with a horizontal, microprocessor-controlled reciprocating plastifier.
Machines in over 50 countries worldwide - Supported from the USA, UK and Italy.
Machines used in and around clean rooms for pharmaceutical production.
Jomar supplies the complete package: Machines, water units and fully guaranteed moulds.
|
|
|
|
|