|
|
Low Power Gas Sensors
|
|
Cambridge CMOS Sensors (CCS) is an industry leader in sensor technology for environmental sensor solutions for a wide range of applications. We are a leading supplier of CMOS MEMS Micro-Hotplates which provide the key technology platform for chemical resistive, and catalytic, gas sensors. This technology uses standard CMOS processes, making it ideal for high volume applications, in terms of scalability and cost.
Limitations of Classic MOX Gas Sensors
Classic MOX gas sensors are large and expensive, have high power consumption and suffer from the following limitations:
Cross Sensitivity - Generally non-specific and react to a multitude of gases
Drift - The baseline and sensitivity will vary from sensor to sensor and over time
Stabilisation - The stabilisation time is several hours to days before they reach a stable baseline
To counter these limitations, expensive and frequent calibration is needed. In addition, expensive filters are required to reduce cross sensitivity.
The Cambridge CMOS Sensors Technology Advantage
Our miniature gas sensors use a unique silicon platform with advanced sensing materials, which:
Reduces the baseline stabilisation time to a few seconds
Greatly reduces cross-sensitivity and enhances selectivity of gases
Enables ultra-low power consumption for portable handheld devices
Our patented CMOS MEMS Micro-hotplates technology provides the key technology platform for our Metal oxide (MOX) gas sensors by enabling sensor miniaturisation, significantly lower power consumption and ultra-fast response times for a wide range of applications.
Our Micro-hotplates are suspended in a high reliability membrane and act as heater elements for a metal oxide-based sensing material. The Micro-hotplates contain electrodes that measure the resistance of the sensing material. Reactions to target gases cause material resistance changes at temperatures between 200oC to 400oC.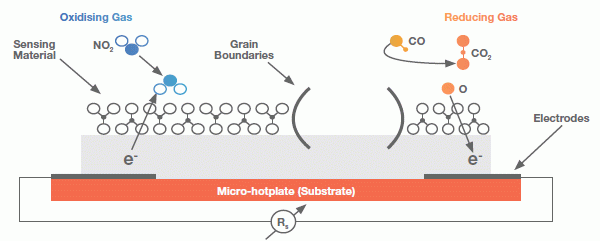 For reducing gases such as Carbon Monoxide (CO) a reaction takes place with the pre-adsorbed oxygen of the sensing material which decreases the resistance of the sensor. For oxidising gases such as Nitrogen Dioxide (NO2) the resistance increases. The magnitude of the resistive changes depends on the metal oxide composition/structure and the operating temperature of the sensor. Figure 1 illustrates the MOX gas sensor structure and how the resistance of the sensing material changes when gas molecules react on the surface.
The relationship between sensor resistance and the concentration of the target gas is non-linear and can be expressed by the following equation over a certain range of gas concentration: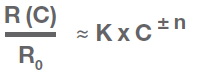 Where
R(C) is the resistance of the film at gas concentration C
R0 is the resistance at zero gas concentration
K is a sensitivity parameter measurement constant
n is a parameter that varies in the range 0.3 to 0.8
The positive sign is used for oxidizing gases and the negative sign is for reducing gases
Advanced algorithms support our family of MOX gas sensors for maximum selectivity, drift compensation and for self-calibration, enabling easy and timely integration into a wide range of applications. |
|
|
|
|