|
Automatic Rim Rolling Machine from WM Wrapping Machinery SA
9/25/2015 |
|
|
Continuing the roundup of machine accessories, built by WM Wrapping Machinery SA, to optimize the production of thermoformed articles, today we examine the groups' automatic rim rolling machines for conical cups and containers.
These rimming units are widely used in the production of disposable cups, which can be made from various materials: Polystyrene, Polypropylene, APET or PLA.
Disposable cups, in most cases, are required to have a rolled rim around the upper part, the mouth, of the cup. This operation rounds off the edge, folding the lip under the rim, to make contact with the lip more comfortable when drinking from the cup and giving the cup greater rigidity at the same time.
Disposable thermoformed plastic cups can be produced on thermoforming machines known as "form-punch" machines i.e. performing the process of forming and punching out the perimeter of the cup simultaneously in the same station. These machines have a tilting lower half-mould which rotates by 75 degrees, allowing the automatic extraction of the products from the mould, their stacking and transport, in a continuous feed, to the subsequent operations of the line. Or alternatively, using a thermoforming machine with a large forming area in combination with a separate high speed horizontal trim press for cutting the perimeter of the cups, which is therefore secondary to the forming stage.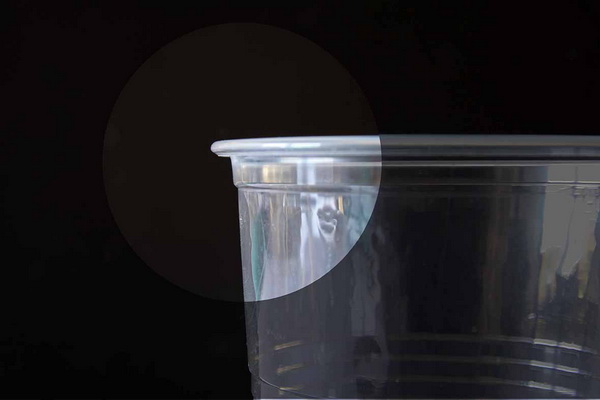 The selection of one system rather than the other is related to the raw material that will be used. Polystyrene has good dimensional stability and a very low shrinkage rate during cooling and this allows the cups to utilize the separate second stage trim press option. For polypropylene it is necessary to form and cut in the same station, to avoid inaccuracies in the perimeter cut due to shrinkage of the material during cooling that can occur between the forming station and a separate trim press.
There are also plants defined as "in-line", with very high production capacities, which also incorporate the sheet extrusion process. These lines start with the raw material in granules and finish with the packaging of the finished product. So it's therefore a true production island.
WM Wrapping Machinery SA designs and manufactures both of these production systems described above.
In the case of the most common, 200cc disposable cups, a line for polypropylene produces about 125,000 pieces/hour while a line for polystyrene can' reach up to 200,000 cups/hour.
It goes without saying then that WM has created two different types of automatic rimming machine, each intended for one of the two types of lines described above and each adapted to the characteristics of the material to be processed. So to put it more simply, one rim roller for polystyrene cups and another for polypropylene and PET.
The two units differ mainly in the length of the rim-rolling screw (longer for polypropylene cups and shorter for polystyrene cups) and also the system of infrared heating which, for the polystyrene is housed in a tunnel before the entrance of the cups into the rim-rolling cylinders, and for polypropylene the heating extends along the length of the three rim-rolling screws, creating a closed chamber through which the stack of cups passes.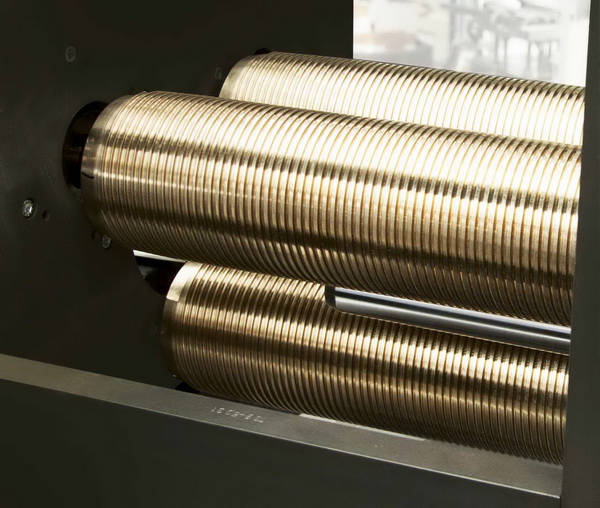 Once rimmed the cups exit from the screws and are automatically transported by a conveyor belt to the downstream units for counting, film sleeving and subsequent boxing operations.
When the cups come out from the punch and die mould or in-line trim press, the upper edge is formed into an inverted U shape. The size and thickness of this edge are critical and must therefore be carefully considered when the mould is made and these parameters must be constantly maintained during the thermoforming process to ensure a perfect flange and an adequate uniform aesthetic appearance.
The rim-rolling screws are obviously the heart of the system and the profile of the grooves that constitute the thread of the screw are produced according to the type of cup, the stacking step and the material with which the cup has been formed, taking into account the dimensional shrinkage of the material.
It should be considered that there is a very wide range of cups with different diameter openings, just think of the difference between the classic coffee cup and a glass of beer. For this reason, the rim-rolling screws can easily be changed according to the design of the cup and readily adjusted in relation to the cup's diameter. The rimming machine can be quickly retooled by the operator in a few simple steps, to make fast, easy and safe production changes.
WM Wrapping Machinery SA has more than twenty years experience in the design and application of these ancillary units, which complete its thermoforming machines, whether they are in the "in-line" with extruders or "off-line" fed from material on the reel. |
|
|
|
|
|